Capacity Planning, Strategies, Benefits and Best Practices
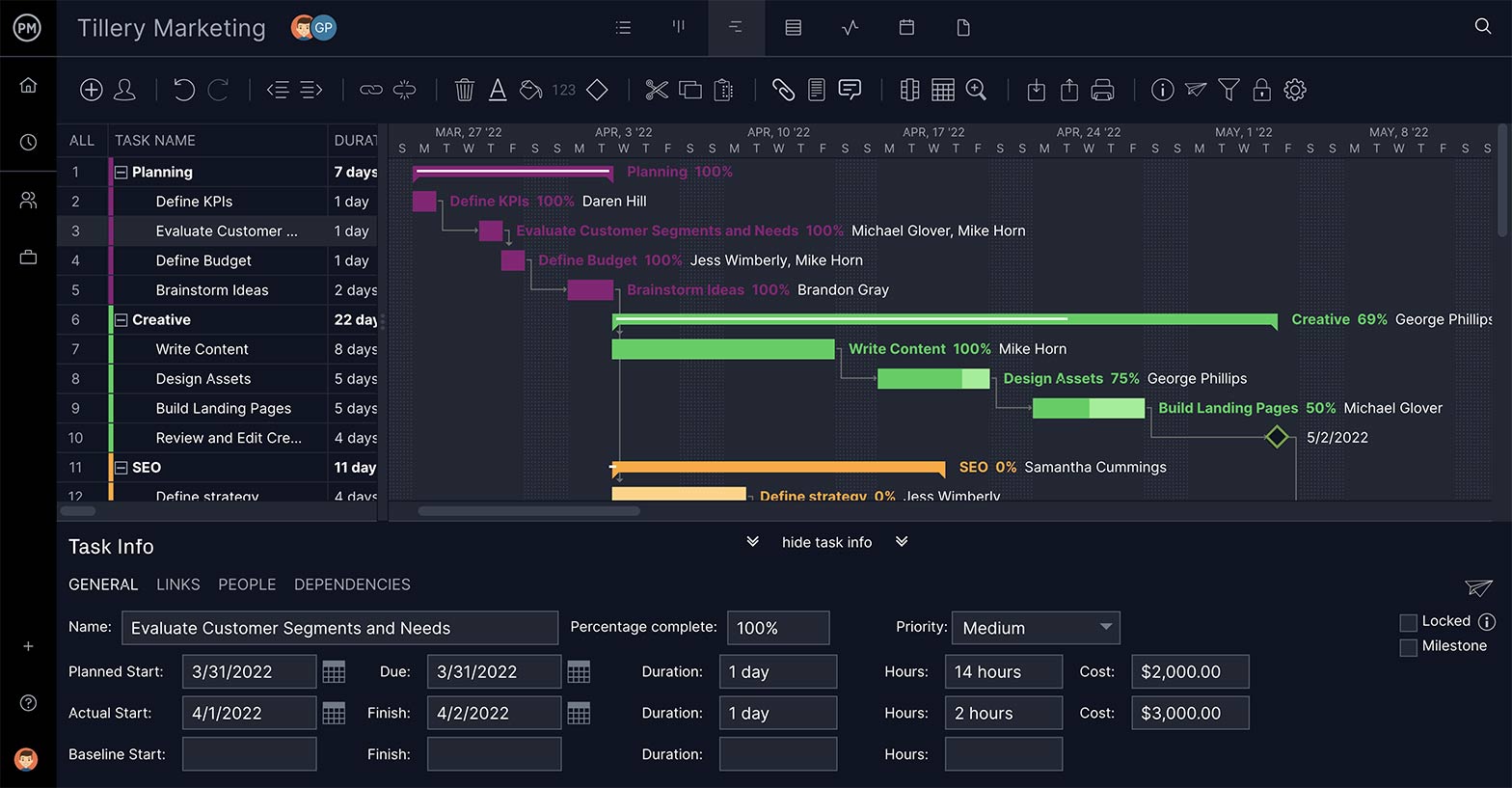
Production capacity planning is an issue of supply and demand: one that can decide the fate of your project or production line. Read on to learn about the capacity planning strategies and capacity management best practices you can use to plan your resources and make sure your team members are working on the right task at the right time.
What Is Capacity Planning?
Capacity planning is a process that balances the available resources to meet customer demand or the project capacity requirements. Capacity, in project management and manufacturing terms, is the most work that can be done over a certain timeframe.
In project management, the capacity planning process is very important because it’s related to critical project management knowledge areas such as:
- Resource management
- Time management
- Team management
- Work management
Production capacity, strategic planning and project planning go hand-in-hand. Planning is how one schedules the hours of the team members so that the work gets done on time. Capacity management isn’t a rigid process. All companies are different and demand can be volatile, so there are different capacity planning strategies that project managers can use to adapt to different scenarios.
ProjectManager is the one project management software that has everything you need for project and capacity planning. With robust Gantt charts and resource management tools, you can build a project schedule that incorporates real-time team availability. Your team can then execute the work in multiple views and you can track what matters with dashboards and project reports. Get started today for free.
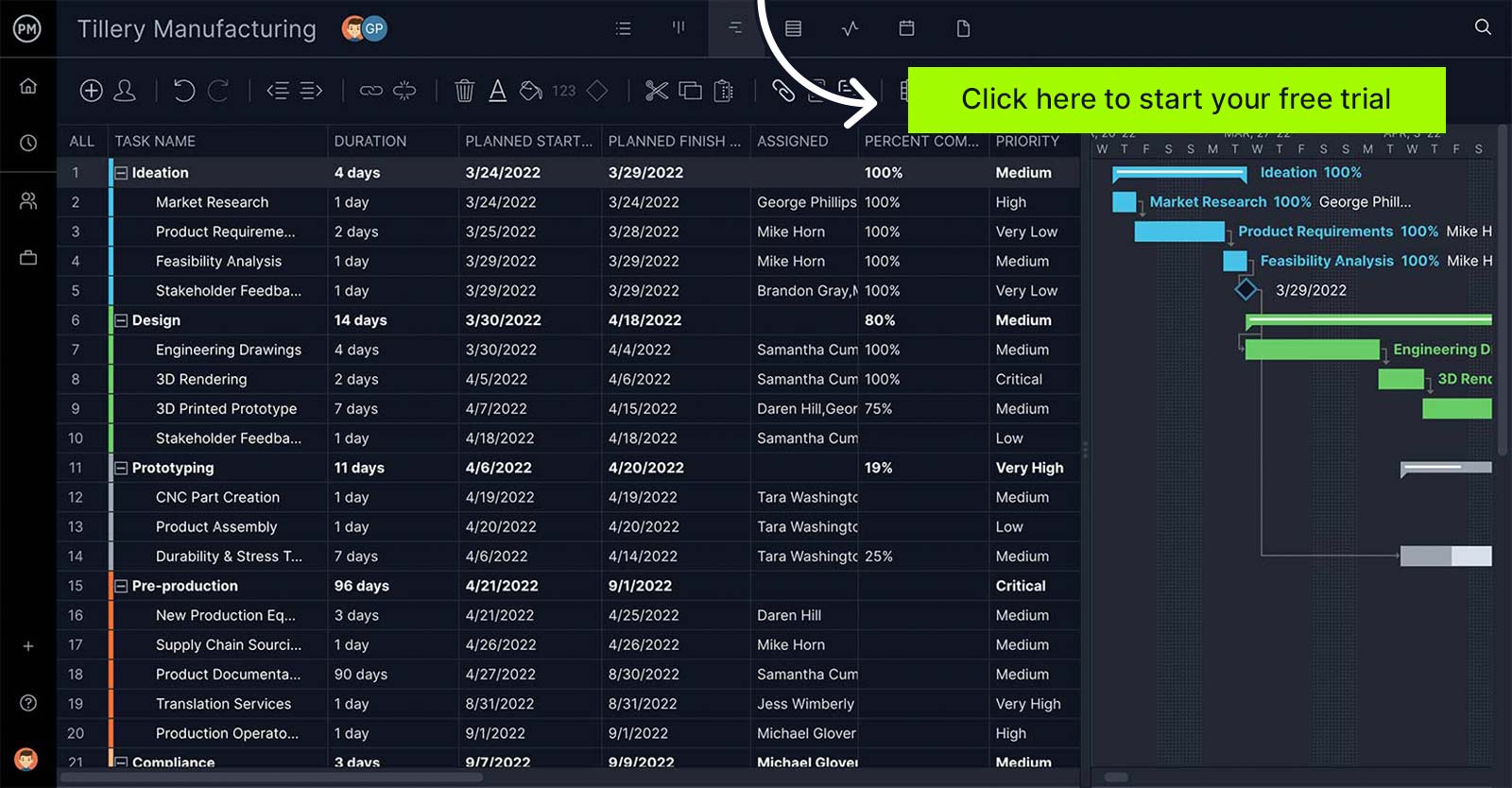
Capacity Planning In Operations Management
As defined, capacity planning is used to determine the amount of work an organization can do over a specific time period. Operations management is about the planning, organizing and controlling of resources to deliver products and services.
Therefore, capacity planning is a critical aspect of operations management as it helps determine what must be done to meet the demand for that product or service. It also sets up a company to grow, while avoiding idle resources and underused capacity.
Capacity Planning In Project Management
Project management is the planning, managing and controlling of work over a determined time that results in a deliverable. This is achieved through the execution of tasks that require both human and non-human resources.
Capacity planning is a critical component of project management as a project schedule and budget are created. It helps project managers figure out the necessary capacities in terms of those resources, especially team members, to meet the project deadline and stay within budget.
Capacity Planning In Production Management
Production management is the process of turning raw materials, human resources and capital into a production output. It involves planning and controlling industrial processes to make sure production runs smoothly.
Capacity planning fits into this process in three ways. There’s production capacity planning to make sure you have enough product or materials for deliverables. Workforce capacity planning deals with your human resources and work hours, while tool capacity planning ensures that your workers have what they need to do their jobs.
Why Is Capacity Planning Important?
Capacity planning is important as it ensures a business has what it needs when it needs it to fulfill demand. It allows for flexibility to help make a wide range of products and, done properly, it’ll make sure that no extra money is spent on the effort.
Budgeting and scaling are both guided by capacity planning, which helps to identify optimal levels of operations. For example, you can determine who services are offered and what the timeframe and staffing requirements will be so you can cover your operational costs.
Beyond those reasons, capacity planning helps managers make more informed decisions. It also helps employees by avoiding burnout or boredom on the job. As mentioned, it’s crucial to help a company grow and assists in making better staffing decisions.
What Does a Capacity Planner Do?
Capacity planning is usually the responsibility of a capacity planner. They’re the ones who plan, analyze, balance and allocate resources as needed to meet the requirements and priorities of the organization. They also respond to customer demand, determining the workforce and timeframe of production to meet that demand.
Depending on the size of the organization, this position can be folded into a project manager’s responsibilities. If it’s a standalone position, however, the capacity planner works with the executive team and other stakeholders. They require excellent communication skills to work well with these different departments.
The capacity planner is a results-oriented person, with strong statistical and reporting skills. They have to collect and understand project data as well as know the trends that are impacting their industry to do their job well.
What Is a Capacity Plan?
A capacity plan is used to achieve the goals of the overall capacity planning of an organization. One of the purposes of a capacity plan is that it can help to avoid scope creep in a project. Scope creep is when the requirements of a project increase over time.
When you create a capacity plan for one project, it can often be used as a template for other projects you’re planning. It helps you quickly identify what you do and don’t need, rather than trying to always go back to forecasting capacity requirements from scratch.
Since capacity planning is about the supply and demand of resources, your capacity plan can help you know when demand will increase or decrease so you can adjust the plan accordingly. Your capacity plan and resource plan will be very much related.
Capacity Planning Process
We’ve explained what capacity planning is and why it’s important. The next step is to understand the process. Capacity planning is done differently from company to company and industry to industry, but it always follows these four basic steps.
Capacity Forecasting
The first step is to understand the demand in order to start planning your capacity to meet that demand. You’ll need to make estimates on what needs to be done for an upcoming project. Use expert advice, historical data and anything else that’ll help you know the capacity you need to complete your project.
Capacity Scheduling
Once you’ve forecasted capacity, you’ll begin the process of creating a production plan. It should include all operations needed to meet customer demand. To do this means scheduling resources, whether raw materials, labor, machinery, etc., to ensure you have the resources needed to complete the project.
Capacity Tracking
To keep to your capacity schedule, you’ll need to track your resources as you go into production. This involves monitoring your non-human resources and making sure you have the inventory needed for the jobs coming up, but also knowing the availability of your human resources so they can be assigned work to complete those orders.
Capacity Reporting
To help with tracking and keeping stakeholders informed of progress, capacity reporting is necessary. A capacity report shows the capacity to deliver and take on new work. These metrics are shown in hours or as a percentage. Reports will also compare your planned capacity with your actual capacity to help you stay on track.
Types of Capacity Planning
There are three types of capacity planning: workforce capacity planning, product capacity planning and tool capacity planning. Each focuses on a different aspect of your project resources. The definition of each of these is listed below.
Workforce Capacity Planning
Workforce capacity planning deals with your human resources. It requires you to figure out the total hours you’ll need to work on a project per week. To find this number, multiply the number of workers you have on the project by the number of hours they work per week. Use this capacity planning formula: (Workers) x (Shifts) x (Utilization) x (Efficiency).
Product Capacity Planning
Product capacity planning is used to figure out production capacity to meet the changing demand for a product. It allows you to make sure you have the materials and labor on hand to create the number of products necessary to respond to the market demand and change production to respond as demand goes up or down.
Tool Capacity Planning
Tool capacity planning helps to forecast how many resources you’ll need and how to allocate those resources at the right time. In short, it makes sure you have the right tools and the right amount of tools necessary to do your job. These tools can include machinery, vehicles, assembly line parts, etc.
Capacity Planning Example
To get a better handle on capacity planning let’s imagine that you’re a retailer and the holidays are approaching. You’ll need to plan in accordance with the expected increase in demand. That will mean a number of things.
First, you’ll look at past seasons to see how many items you sold and compare that to market demand presently to forecast your expected demand. Once you have that figured out, you’ll need to reach out to suppliers and make sure you have access to the increased amount of items you need to stock for that demand.
Now, you’ll want to look at your labor force. You may need to increase workers. It’s not uncommon for retailers to hire seasonal workers to handle the expected influx of customers over a holiday period.
Finally, you’ll want to make sure you’re tracking the items sold and the items you have warehoused. This will help you get a more accurate reading on demand and will help you restock before you run out of inventory, which could lead to lost sales.
Capacity Planning Strategies
There are three capacity planning strategies to help you meet demand, cover your resource requirements and increase your team members’ productivity.
Lag Strategy
The lag strategy consists of having enough resources to meet actual demand, not projected demand estimates. This capacity planning strategy is beneficial for smaller organizations that have low capacity requirements.
Lead Strategy
The lead strategy consists in having enough resources to meet demand planning forecasts. This capacity planning strategy is beneficial when demand increases, as your excess capacity can cover the increased demand.
Match Strategy
This strategy is a mix of the lead and lag capacity planning strategies. In this case, project managers need to monitor actual demand, demand planning forecasts and market trends to adjust capacity accordingly.
Capacity Planning Benefits
Production capacity planning is an important strategic planning process for many reasons. Here are some of the main benefits of effective capacity planning.
- Reduces costs
- Prevents stock-outs
- Reduces production lead time
- Eliminates excess capacity
- Helps with supply chain management: A clear understanding of your project capacity requirements helps you get the right amount of resources, which benefits your supply chain.
- Helps with resource management: Having the right production capacity to meet your capacity requirements is key to optimizing resource planning and resource allocation.
Capacity Planning vs. Resource Planning
While the terms “capacity planning” and “resource planning” are sometimes used interchangeably, they’re not the same. To understand the differences, we’ve listed them below.
Capacity Planning
- It’s a strategic planning process designed to help determine if the organization has the production capacity required to meet the demand
- It looks at resource availability at the skill set/team level
- Then it facilitates the decision-making process to hire resources or defer/approve/cancel projects
- Capacity planning is about supply and demand
Resource Planning
- It’s a strategic planning process that coordinates and allocates actual resources to project tasks based on resource requirements
- It provides a plan to project managers, which resources they can plan to use for their projects and when
- Resource planning focuses on resource allocation
Related: Free Resource Plan Template
Capacity Planning vs. Capacity Requirements Planning
Capacity requirements planning is the step before capacity planning. It’s the process when an organization decides how much it needs to produce and whether it has the production capacity to be capable of doing so.
Capacity Planning Best Practices
Here are some tips and capacity planning best practices to help you manage your resources and teams.
- Establish a cross-functional team: To collaborate and communicate about production capacity and resource management, you want a cross-functional team with different levels and different functions.
- Calculate resource capacity: Before you can create a production capacity plan, you need to have an idea of your current capacity and your available resources.
- Determine resource requirements: For each project, look at the scope and what resources are required to do the task for the project.
- Prioritize projects: Which projects are most important, and which can be put aside for the time being? You can’t do everything at once.
- Allocate resources based on project priority: Now allocate those prioritized projects and ensure they’re aligned with the goals of the organization.
- Keep the lines of communication open: Communicate between executives, project management leaders and stakeholders.
- Document known risks: Monitor risks such as union strikes, weather and government regulations that stop a project or create new ones unexpectedly.
- Plan for how to handle too much capacity: Understand where it is and how to resolve it (such as reassigning), or not enough capacity (again, where/how).
ProjectManager Is a Great Capacity Planning Tool
Capacity planning requires the right resource management tools to give managers insight into their production capacity. ProjectManager is online project management software that gives them real-time data to make real-smart business decisions.
Our resource management tools provide a window into your team’s resources and help you plan better on our online Gantt charts. To get a full picture of the costs involved, you can add hourly rates for your teams and contractors across your project or portfolio. As team members log their hours, their actual costs are automatically calculated and can be compared to the costs that were planned.
Capacity Planning Video
Want to learn more about capacity planning? Watch the video below from Jennifer Bridges, PMP. Although her video focuses on IT teams, capacity management lessons can be applied to any industry.
Here’s a screenshot for your reference!

Thanks for watching!