Understanding tubefalire/Failures: Causes, Prevention, and Maintenance
Tube failures or tubefalire are a significant concern across various industries, including power generation, manufacturing, and healthcare. These failures can lead to operational disruptions, safety hazards, and increased maintenance costs. This article delves into the common causes of tube failures, effective prevention strategies, and maintenance practices to ensure optimal performance and longevity of tube-based systems.
Common Causes of Tube Failures/ tubefalire
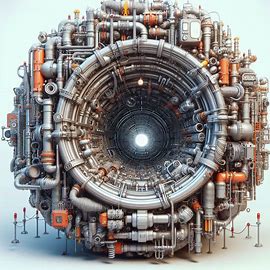
- Corrosion: Corrosion is a primary cause of tube degradation. Factors such as oxygen pitting, sulfidation, and the presence of corrosive agents can lead to localized attacks on the tube material, resulting in thinning and eventual failure. For instance, oxygen pitting occurs when excess oxygen in the boiler water reacts with metal components, leading to corrosion.
- Overheating: Excessive temperatures can weaken tube materials, causing them to lose structural integrity. Short-term overheating often results from sudden stress ruptures, while long-term overheating can lead to creep damage. Both scenarios compromise the tube’s functionality and safety.
- Fouling and Scaling: The accumulation of deposits, such as minerals or other particulates, on the inner or outer surfaces of tubes can impede heat transfer. This buildup not only reduces efficiency but also creates hotspots that may cause tube failure.
- Mechanical Stress: Factors like frequent start-ups and shutdowns, rapid load changes, and improper handling can introduce mechanical stresses. These stresses may lead to fatigue, cracking, or rupture of tubes.
Preventive Measures
To mitigate the risk of tube failures, consider implementing the following strategies:
- Regular Maintenance and Inspection: Conduct routine checks to identify early signs of wear, corrosion, or deposit buildup. Timely detection allows for corrective actions before failures occur.
- Water Treatment Programs: Implementing effective water treatment protocols can control the quality of water used in systems like boilers, reducing the risk of corrosion and scaling.
- Material Selection: Choose tube materials that are compatible with the operating environment and resistant to specific corrosive agents present in the system.
- Operational Controls: Maintain stable operating conditions to minimize mechanical stresses. Avoid rapid temperature and pressure fluctuations that can strain tube materials.
Maintenance Best Practices
- Cleaning: Regularly remove deposits through chemical or mechanical cleaning methods to maintain efficient heat transfer and prevent fouling-related failures.
- Protective Coatings: Apply corrosion-resistant coatings to tube surfaces as an additional protective barrier against corrosive agents.
- Monitoring Systems: Utilize advanced monitoring technologies to track parameters such as temperature, pressure, and corrosion rates, enabling proactive maintenance decisions.
Conclusion
Understanding the causes and preventive measures associated with tube failures is crucial for maintaining the reliability and safety of industrial systems. By implementing regular maintenance routines, adopting effective water treatment programs, selecting appropriate materials, and ensuring stable operational practices, industries can significantly reduce the incidence of tube failures and enhance overall system performance.
- Photoaxompa: Ancient Mexican Art and Healing That’s Shaping Modern Wellness
- Discover the Impact of Hosted Event Pblgamevent: A Hub for Gaming Enthusiasts & Professionals
- From Startup to Scale: How Strategic Partnerships Propel Business Growth
- Email Marketing Ideas to Shake Your Business Up! cleverscale.com in 2025
- Ron Leonhardt Jr. – Net Worth, Age, Bio, and Wiki